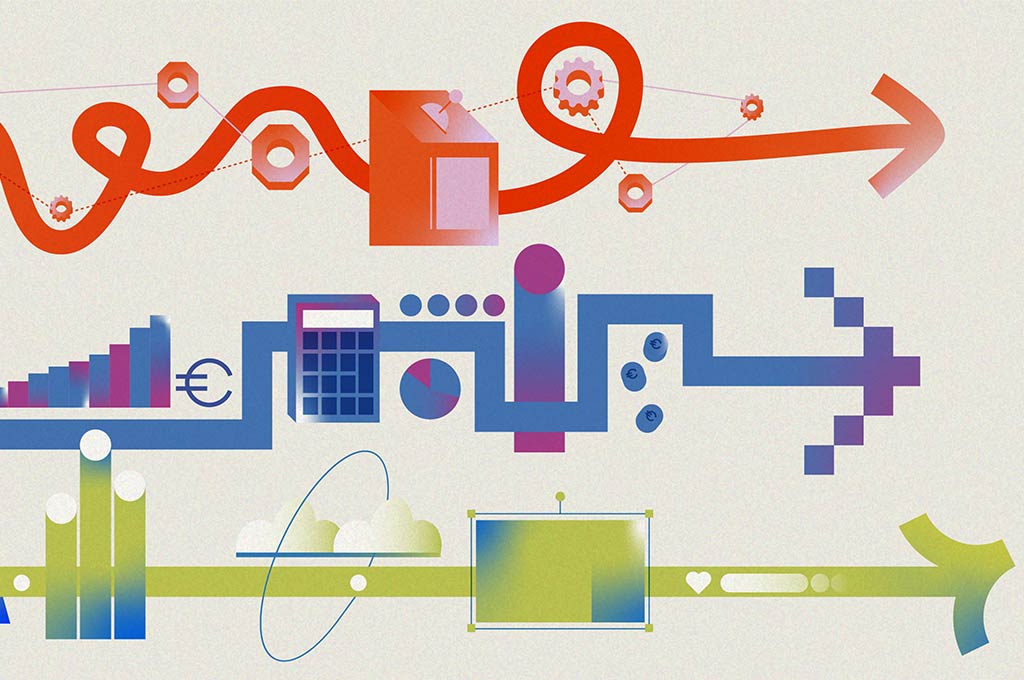
IESE Insight
Make it agile: how agile manufacturing can democratize access to high-tech production capabilities
Make it yourself or buy from a supplier? Now there’s a third choice — opting for agile systems — which, for smaller manufacturers, might be the better way to stay competitive.
By Joan Jané
Changing consumer preferences. Shorter product life cycles. Greater customization. Today’s fragmented, fast-changing market dynamics are seeing a shift away from traditional mass production toward more adaptive, flexible systems in order to remain competitive and resilient in this new, more volatile environment. In short, it’s time for manufacturers to get agile.
Agile manufacturing is deeply intertwined with the rise of Industry 4.0 technologies, including cyber-physical systems, the internet of things, big data and artificial intelligence (AI). These innovations enable firms to optimize their supply chains, improve production efficiency and meet urgent sustainability goals. They also allow companies to produce low-volume, high-quality products that cater to specific customer needs, thereby addressing the growing demand for individualized products.
For example, a healthcare products manufacturer might use 3D printers to custom-make everything from dentures and hearing aids to bespoke body parts for doctors to practice on before surgery. Or an automotive company might connect its assembly lines to a single information system to track production, anticipate bottlenecks and trace missing parts. It might employ AI sensors to check products automatically and flag potential defects to human inspectors, as well as using RFID tags for end-to-end traceability and synchronized workflows. Drones equipped with thermal cameras could find leaks, helping to prevent wasted energy. These are just a few of the many different Industry 4.0 applications.
Agile manufacturing is especially important in Europe, with two initiatives — the Digital Decade Policy Program for 2030 and the Horizon Europe program until 2027 — aimed specifically at boosting EU competitiveness and growth by encouraging R&D and investment in advanced manufacturing technologies. Unfortunately, progress so far has been slow, with Member States reportedly falling short of targets or trailing behind international competitors in their adoption of these technologies.
One reason may be the high number of SMEs in Europe. Smaller, resource-constrained firms may fear the extra costs and risks involved, but, in reality, they stand to benefit the most from agile manufacturing’s flexible, pay-per-use business models, which actually lower capital expenditures and mitigate risk.
Based on a literature review as well as focus groups with industry professionals, especially those in the automotive, aerospace and medical sectors, I identify how agile manufacturing can democratize access to high-tech production capabilities. For those struggling with their own make-or-buy decision, agile may be the answer.
Make or buy?
For manufacturers, the traditional make-or-buy decision has always been a critical one, with each option having its pros and cons.
- Do I make it myself? If I choose this option, I may have to invest in the machinery and infrastructure required to produce the parts in-house. This decision typically involves high upfront capital expenditure and investment in technology, equipment and skilled labor. On the upside, doing it myself also provides greater control and oversight of production, ensuring quality and flexibility in adapting to new market demands. By retaining full ownership of production, the risks are internalized and can be better mitigated, which is beneficial in high-risk sectors like aerospace and automotive.
- Or do I buy it? If I choose to buy, I outsource production to third-party suppliers, leveraging their capabilities instead. For situations in which demand is inconsistent, seasonal or project-based, or when the capabilities required are beyond what my own company can handle internally, this can be the more efficient choice. This lowers or completely avoids upfront costs of production, eliminating the need for acquiring expensive machinery or assuming the associated operational costs myself. However, while outsourcing noncore activities enables me to focus on my core competencies, it also means I lose control over key processes and potentially become reliant on external partners for a component vital to my business.
Evidently, either of these decisions brings associated trade-offs regarding control, cost, quality, flexibility and risk. Thankfully, these aren’t the only two choices: there is another strategy that companies must assess beyond the traditional make-or-buy one, and it’s related to the introduction of agile manufacturing.
Agile manufacturing, a third way
Agile manufacturing introduces a new decision-making element that shifts the traditional make-or-buy dichotomy. With the rise of cloud-based agile systems, companies can choose to make parts without incurring all the usual costs associated with “make” decisions. The following are among the key factors:
- Reduced capital investment: Agile manufacturing technologies offer pay-per-use models that minimize the need for costly capital expenditure (CapEx) investments. Companies can access high-end manufacturing technologies without purchasing machinery outright.
- Speed and flexibility: Agile processes reduce the time needed to bring new products to market, allowing companies to remain competitive even when demand rapidly shifts.
- Risk mitigation: By utilizing agile systems, companies can experiment with new products and processes with minimal risk. If demand fluctuates, they can scale production up or down without being locked into long-term investments.
- Short lead times: Agile technologies, such as additive (3D) manufacturing, enable much shorter lead times for production. This helps companies reduce the time to market for customized and small-batch products.
- Project-based demand: Agile manufacturing allows manufacturers to meet short-term or seasonal demand spikes without needing to purchase new equipment. Companies can scale production as needed for the duration of the project, ensuring flexibility and cost-effectiveness.
Core considerations for agile
This is not to say that agile is always the better choice. In my research of manufacturers, I surfaced several key factors influencing the adoption or non-adoption of an agile manufacturing business model. In general, the decisive factors can be grouped around:
- Your in-house capabilities: For companies that already have strong internal teams trained in cloud operations or have well-established IT infrastructures, the agile manufacturing model may be less attractive. However, for those without these capabilities, agile manufacturing offers a plug-and-play solution that eliminates the need for extensive internal training and development.
- A high level of experimentation required: Agile systems allow companies to experiment with new designs and production processes without heavy capital investment, enabling innovation without long-term risk.
- Rapid turnaround times: When lead times are short, agile pay-per-use models can be more favorable than traditional manufacturing processes.
- Seasonal demand: An agile model allows you to avoid the costs of maintaining underutilized equipment by paying only for what you need when you need it.
Risk and financial considerations
Having laid out the conditions favoring agile manufacturing, this is not to say that agile is without risks nor that “financial flexibility” means no capital expenditure will be involved. There may well be upfront costs, and because Industry 4.0 technologies are evolving so fast, the risk of them quickly becoming obsolete is real.
That being said, it is fair to say that companies can scale their production based on real-time demand without tying up capital in equipment purchases. And for companies concerned about the resale value of machinery, agile manufacturing offers a lower-risk alternative because it avoids the risk of depreciating assets. The pay-per-use model allows companies to remain nimble and adjust to changing market conditions without being locked into expensive long-term investments.
Moreover, given today’s currency fluctuations, rising energy costs and dynamic economic conditions, the strategic value and cost structure of each decision can have profound long-term effects on a company’s operational capabilities and competitiveness.
Innovating new business models
Crucially, any solution must be aligned with your organizational model and specific business needs — managing expenditures strategically, focusing on your employees, and involving the procurement function in product development. Working in close collaboration with vendors and nurturing long-term, value-adding relationships are other key requirements, regardless of whether you adopt agile manufacturing or go the traditional route.
Additionally, everyone agrees that regular innovation is essential for success, linked as it is to continuous changes in the environment. As such, most manufacturers are looking to evolve their business models to automate more processes, to be more flexible and responsive to market needs, and to implement more cutting-edge solutions. And these are precisely the features in which agile manufacturing excels.
Particularly for EU manufacturers that are seeking not only to remain competitive in the global marketplace but to innovate and adapt to evolving market demands, agile manufacturing is a recommendable strategy. The old make-or-buy decision may have a new answer: choose agile.
SOURCE: “Agile manufacturing” by Joan Jané and Holly Anne Hill is published by IESE in association with the Agile Manufacturing Society.
This article is published in IESE Business School Insight magazine #169 (Jan.-April 2025).