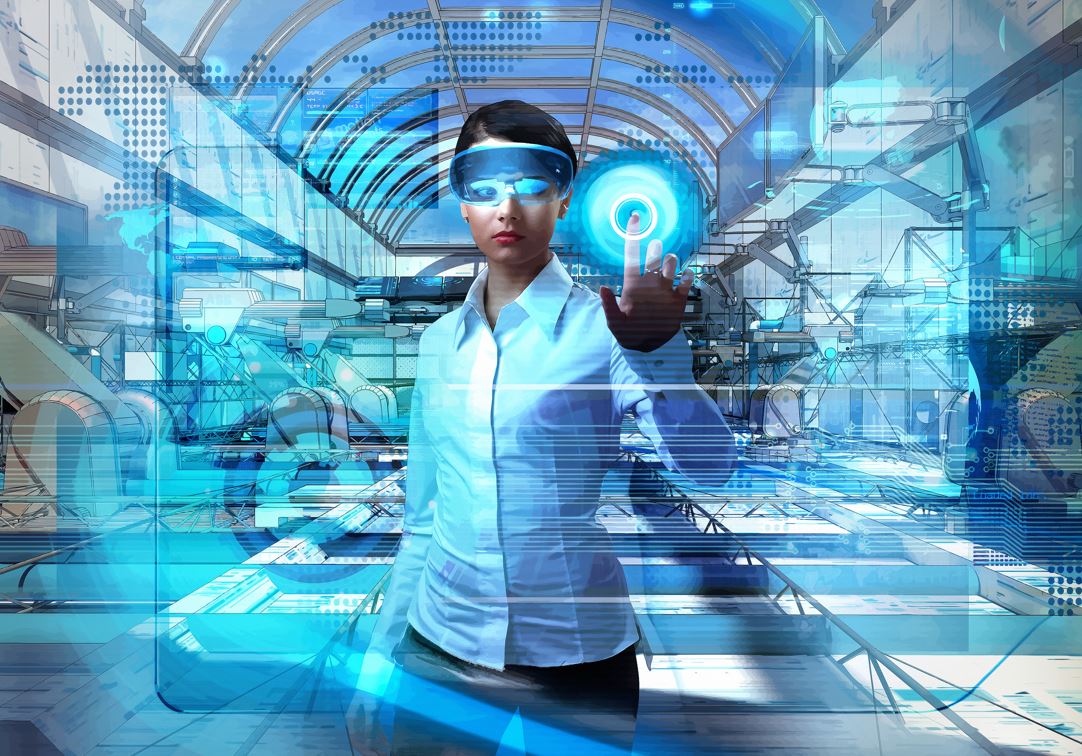
IESE Insight
5 building blocks for cyber-physical value chains
Digitalization is disrupting manufacturing as it did services. Here’s how companies must adapt to protect their value chains and stay competitive.
By Marc Sachon
During the global financial crisis, countries with a solid manufacturing base suffered less than service-based economies. This was certainly the case for Germany, whose Mittelstand of small and medium-sized firms, many of them manufacturing-based, were able to maintain or increase employment, or even expand, during the crisis.
Recognizing that manufacturing contributes greatly to job creation and innovation, the German government laid out its future industrial policy in 2011, called Industrie 4.0, a term which has since entered the vernacular. Other countries are following suit, including the United States, with recent administrations aiming to re-industrialize the economy.
Based on interviews, case studies and collaborations with firms at the leading edge of this field, I have identified the key building blocks for the successful implementation of Industry 4.0, which I share in this article. I also highlight the implications, including a need for re-education of the labor force. For industrial companies, the need is clear: their business models are about to change radically, and they must adapt their skill sets to the digital world or get left behind.
A brief history
Industry 4.0 is a natural progression of past industrial revolutions — starting with the mechanization of manual labor in the 18th century, and continuing in the 21st century with smart, interconnected machines that act independently to manufacture products in highly flexible, reconfigurable systems. Let’s review:
Industry 1.0. The first industrial revolution occurred around 1776, when steam engine power was harnessed in factories, replacing manual work and moving away from rivers and closer to markets or ports. This reduced costs while significantly increasing productivity, particularly in textile manufacturing, a sector that was instrumental in this phase.
Several sectors were disrupted, leading to high levels of unemployment, such as when automated looms displaced manual ones. It also led to a concentration of manufacturing capacity in industrial clusters, which generated population movements from rural areas to those clusters, and gave rise to changes in society, from the emergence of politically powerful industrialists, to the creation of a working class, to the rise of communism.
Despite this revolution, high-quality, complex products — such as watch-making, tailoring or, by the end of the 19th century, car-making — still had to be done by hand, as no machine was capable of making customized products in large volumes at low cost.
Industry 2.0. The second industrial revolution had several triggers: the use of electricity to power factories; advances in material sciences, leading to high-grade steel and interchangeable precision metal parts; and the standardization of work, which shifted specialized skills from workers to machines and tools.
These developments converged in Henry Ford’s moving assembly line (1913). For the first time, high-quality, complex products could be manufactured in large volumes at low cost. The trade-off was a narrow product assortment, but customers didn’t mind, because the products were affordable for the common person.
Apart from limited variants, another consequence of Ford’s conveyor-belt automation was the de-skilling of labor. At the time, this was not a problem: Ford only needed low-skilled labor, and for that, the labor pool was large. The trend started by the steam engine continued: the number of skilled workers declined (in relative terms) and skilled labor moved from the (manual) shop floor to the office.
Industry 3.0. The third industrial revolution had several defining moments. First came the Intel processor
chip in 1971. The emergence of semiconductors allowed process control units to be integrated in machines, and the creation of computer numerical control (CNC) increased machine intelligence and flexibility. With several machines able to be operated at once, fewer workers were needed, and the trend toward more knowledge workers continued.
Meanwhile, the 1970s saw oil and energy crises, which shook up vertical market dynamics. With growth stagnant, markets moved from supply-driven to demand-driven. In such a context, Ford’s system of mass production had difficulty adapting to changing customer preferences.
Toyota’s solution was to change the management focus from maximizing asset utilization (the U.S. philosophy) to minimizing waste (the concept of lean) and maximizing value added per unit of time (the concept of flow), enabling more products and variants to be made, while keeping quality high and costs low. This proved better than mass production, because it accommodated changing customer needs.
Industry 4.0. In the 21st century, the following global trends are pushing production systems to their limits:
- customization: customers want a product adapted to their specific requirements.
- globalization: vast, interconnected supply chains and markets are spread all over the world, increasing management complexity.
- financial markets: institutions are still recovering from the 2008 financial crisis.
- aging workforce: in China, Japan, Russia and Western Europe, the average age of a factory worker is increasing, making certain tasks more difficult for them to perform, thus resulting in lower efficiency.
- sustainability concerns: energy efficiency, waste reduction, and responsible use of natural resources have become priorities.
- growing population and middle class: demographic trends are driving growing demand for certain products (e.g., cars in China).
- information society: in a connected world, new ideas spread rapidly, accelerating the development of new products, processes and business models, and generating difficult-to-serve demand peaks (e.g., iPhone).
- urbanization: people are migrating to cities, while factories tend to be located away from them, making it hard to find qualified workers.
These trends require flexible systems that can change quickly and efficiently. To deal with this, the apparel sector developed the fast fashion model, epitomized by Zara, which my IESE colleague Victor Martinez de Albeniz has written about extensively. It essentially accelerates the supply chain by eliminating wasted time with flexible production. Other sectors with more complex supply chains, such as automotive and aerospace, have been slower to adapt, given a higher asset base and asset specificity, and a lack of technological solutions that would facilitate an equivalent form of “fast industry.” Until now.
Today, smart machines, products and infrastructure can all be connected to collaborate in dynamic ways. This networked model of production — in which all levels of IT systems within a company and across companies in a value chain are connected and share data and information — is the next iteration of everything that came before.
When fully deployed, Industry 4.0 holds the promise of reconfigurable production systems and intelligent, networked tools, machines, facilities and products that communicate among themselves and with the workforce, using augmented reality or other means of communicating relevant data quickly, intuitively and efficiently.
Moreover, smart products and components will provide information, and the production system will automatically adapt to product-specific needs. Tools, machines, facilities and products will contain sensors that provide data necessary for decision-making. Because this can be done in an automated way, people working in this area will focus more on generating value for customers, and less on monitoring machines or production processes.
Five essential building blocks
Industry 4.0 holds implications for value creation, business models, downstream services and work organization. But to reap the benefits, certain building blocks have to be in place. I group these into five clusters.
The full article is published in IESE Insight Issue 33 (Q2 2017).
This content is exclusively for personal use. If you wish to use any of this material for academic or teaching purposes, please go to IESE Publishing where you can purchase a special PDF version of “5 building blocks for cyber-physical value chains” (ART-3012-E), as well as the full magazine in which it appears, in English or in Spanish.