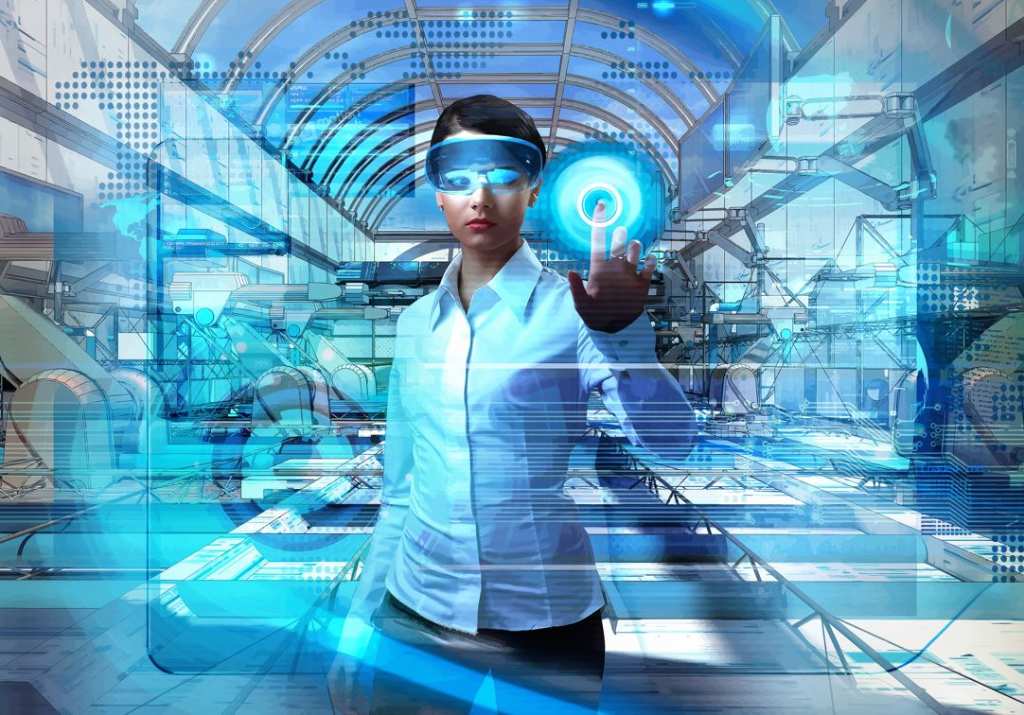
IESE Insight
Los cinco puntales de la cadena de valor en la industria 4.0
La digitalización, que ha tenido un impacto disruptivo en los servicios, está a punto de hacer otro tanto en la industria. Estas son las claves para adaptarse al cambio y proteger la cadena de valor en la industria 4.0.
Por Marc Sachon
Durante la crisis financiera global, las economías con una sólida base industrial sufrieron menos que las volcadas en los servicios. Un caso claro lo tenemos en Alemania, cuyas mittelstand (pymes), la mayoría fabricantes, pudieron mantener o aumentar sus plantillas e incluso expandirse. Consciente de que la industria manufacturera contribuye de forma significativa a la creación de empleo y la innovación, el Gobierno alemán elaboró en 2011 una iniciativa llamada Industria 4.0, un concepto que desde entonces se ha popularizado. Otros países han seguido su ejemplo, como Estados Unidos, donde la reindustrialización de la economía está presente en la agenda política desde la Administración de Obama.
A partir de entrevistas, casos y colaboraciones con empresas a la vanguardia de su sector, se ha identificado los puntos para dar el salto a la industria 4.0, así como sus implicaciones. En el caso de los fabricantes, la conclusión es clara: sus modelos de negocio van a cambiar radicalmente, por lo que deben adaptar sus competencias al mundo digital o quedarán rezagadas.
Un poco de historia
La industria 4.0 es una evolución natural de las revoluciones industriales anteriores, desde la mecanización del trabajo manual en el siglo XVIII hasta la automatización actual. En todas ellas se cuenta con máquinas inteligentes e interconectadas que actúan de forma autónoma para fabricar productos en sistemas muy flexibles y reconfigurables.
INDUSTRIA 1.0. La primera revolución industrial arrancó en 1776, cuando la máquina de vapor entró en las fábricas, sustituyó trabajos manuales y permitió el traslado de las operaciones de los ríos a los mercados o puertos. Se redujeron así los costes, además de aumentar la productividad, sobre todo en el textil, una industria clave en esta fase.
Esta disrupción afectó a varios sectores y provocó altos niveles de desempleo, como cuando los telares automatizados desplazaron a los manuales. También impulsó la concentración de los fabricantes en clústeres industriales y, con ella, la migración de la población rural a esas zonas. Todo ello desencadenó cambios en la sociedad, como la aparición de poderosos magnates industriales, la clase trabajadora y el comunismo.
Pese a esta revolución, los productos complejos y de alta calidad (como los relojes, las prendas o, a finales del siglo XIX, los coches) todavía debían hacerse a mano, ya que no había máquinas capaces de fabricar esos productos en grandes volúmenes y a bajo coste.
INDUSTRIA 2.0. La segunda revolución industrial tuvo varios detonantes: el uso de la electricidad en las fábricas; los avances en materiales, que alumbraron el acero fino y piezas metálicas de precisión e intercambiables; y la estandarización del trabajo, que provocó que las máquinas y herramientas tomaran el relevo de las habilidades especializadas de los trabajadores.
En 1913, estos adelantos convergieron en la cadena de montaje de Henry Ford. Por fin, se pudieron fabricar grandes lotes de productos complejos y de alta calidad a un precio asequible, por lo que a los clientes no les importó la reducción de la variedad.
Otra de las consecuencias de la fabricación en serie fue la descalificación de la fuerza laboral. Continuó así la tendencia iniciada por la máquina de vapor: disminuyó la mano de obra cualificada (en términos relativos) y los empleos que exigían más formación pasaron de la planta a la oficina.
INDUSTRIA 3.0. La tercera revolución industrial estuvo jalonada por una serie de avances decisivos. En 1971 fue el procesador Intel. La aparición de los semiconductores permitió integrar unidades de control de proceso en máquinas y robots, mientras que el control numérico informático aumentó la inteligencia y flexibilidad de las máquinas. La posibilidad de manejar varias máquinas a la vez redujo la necesidad de operarios, lo que acentuó la tendencia hacia un aumento de los trabajadores del conocimiento.
En esa década varias crisis energéticas sacudieron los mercados verticales. La estancación del crecimiento provocó que la demanda sustituyera a la oferta como impulsora del mercado. En este entorno, el sistema de producción en masa de Ford tenía problemas para adaptarse a los cambios en las preferencias del consumidor.
La solución de Toyota fue un nuevo enfoque de gestión que pasó de la maximización del uso de activos (la filosofía estadounidense) a minimizar las pérdidas (el concepto de la fabricación lean) y maximizar el valor añadido por unidad de tiempo (el concepto de flujo). De ese modo, se pudo fabricar más productos y variantes sin perder calidad o aumentar los costes. Al permitir la adaptación a los cambios según las necesidades del consumidor, el sistema lean resultó más eficaz que la producción masiva.
INDUSTRIA 4.0. En el siglo XXI, las siguientes tendencias internacionales están llevando los sistemas de producción al límite:
- Personalización. Los clientes quieren un producto que se ajuste a sus necesidades específicas.
- Globalización. Los mercados y las cadenas de suministro, vastos e interconectados, se extienden por todo el mundo, lo que complica la gestión. Al mismo tiempo, se producen unos picos de demanda de productos globales (especialmente de electrónica de consumo) sin precedentes.
- Mercados financieros. Todavía se están recuperando de la crisis financiera de 2008. Este hecho, sumado al incremento de transacciones de divisas, dificulta la planificación de la producción.
- Envejecimiento de la fuerza laboral. En China, Japón, Rusia y Europa Occidental está aumentando la edad media de los operarios. Les cuesta más desempeñar determinadas tareas, con lo que la eficiencia se resiente.
- Sostenibilidad. La eficiencia energética, la reducción de residuos y el consumo responsable de los recursos naturales son ahora prioritarios.
- Crecimiento de la población y de la clase media. Los cambios demográficos impulsan la demanda de ciertos productos, como los coches en China.
- Sociedad de la información. En un mundo tan conectado, la rápida difusión de las ideas acelera el desarrollo de nuevos productos, procesos y modelos de negocio. También se producen súbitos picos de la demanda difíciles de cubrir, como ha ocurrido con el iPhone.
- Urbanización. Prosigue la migración del campo a la ciudad, pero las fábricas suelen ubicarse lejos, con lo que es más difícil encontrar trabajadores cualificados.
Estas tendencias exigen sistemas flexibles que puedan cambiar rápida y eficientemente. El sector de la moda, por ejemplo, ha desarrollado el modelo de producción prontomoda, representado por Zara y sobre el que mi colega del IESE Víctor Martínez de Albéniz ha escrito abundantemente. En esencia, este modelo elimina los tiempos muertos de la cadena de suministro gracias a un sistema de producción flexible. La adaptación de otros sectores con cadenas más complejas, como el automovilístico y el aeroespacial, ha sido más lenta debido a que requieren más activos y más específicos, y a la falta de soluciones tecnológicas que permitieran una forma equivalente de fabricación rápida. Pero ya es posible conectar máquinas, productos e infraestructuras para que colaboren de forma dinámica. Este modelo de producción en red es la nueva iteración de todo lo visto hasta ahora: todos los niveles de los sistemas de TI de una empresa y de los que componen una cadena de valor están conectados y comparten datos e información.
Cuando esté plenamente desarrollada, la industria 4.0 promete ofrecer sistemas de producción reconfigurables y herramientas, máquinas, instalaciones y productos capaces de comunicarse entre sí y con los trabajadores mediante la realidad aumentada u otros medios para transmitir datos de manera rápida, intuitiva y eficiente.
Además, los productos y piezas inteligentes suministrarán información que permitirá adaptar de forma automática el sistema de producción a las necesidades específicas de cada producto. Herramientas, máquinas, instalaciones y productos integrarán sensores que recabarán los datos necesarios para la toma de decisiones. Como este proceso es automatizable, las personas que trabajen en esta área podrán dedicarse más a generar valor para el cliente que a monitorizar máquinas o sistemas de producción.
Cinco puntales de la industria 4.0
La industria 4.0 tiene implicaciones positivas para la creación de valor, los modelos de negocio, los servicios auxiliares y la organización del trabajo. Pero, para beneficiarse de ello, las empresas deben seguir una serie de pasos, agrupados en cinco áreas.
Una versión de este artículo se publica en la revista IESE Insight 33 (T2 2017).
Este contenido es exclusivamente para uso individual. Si deseas utilizar este material en clase, puedes adquirir las copias que necesites tanto de "Los cinco puntales de la cadena de valor en la industria 4.0" (ART-3012) como de la revista completa en formato PDF mediante IESE Publishing.