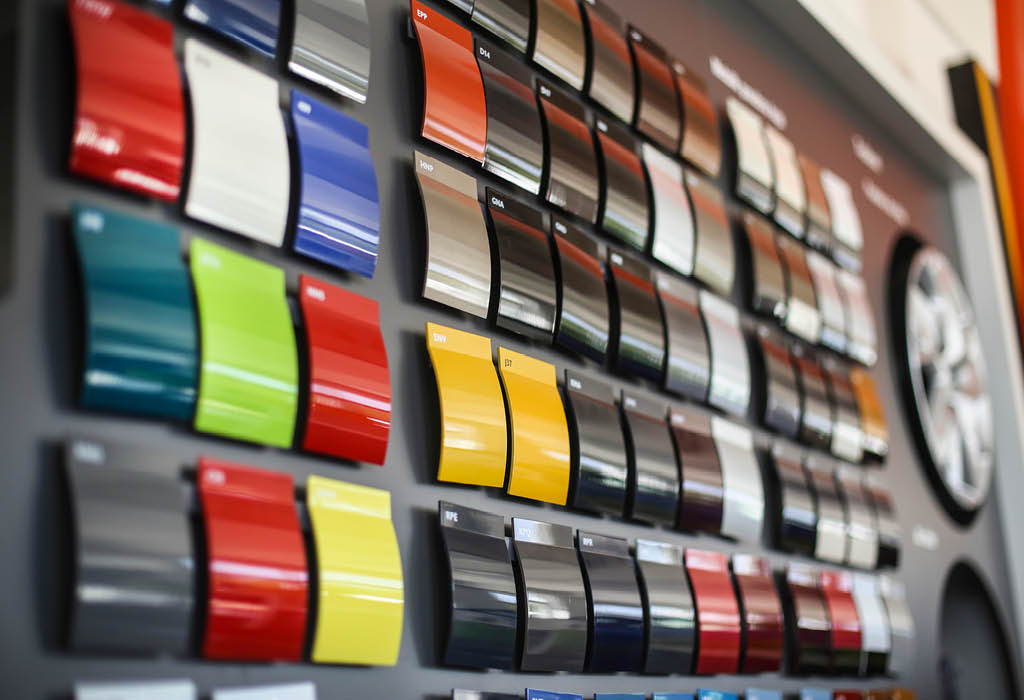
IESE Insight
Adiós a los stocks, bienvenidos los coches a medida
Un coche personalizado para cada cliente. Esta consigna de marketing puede parecer trivial pero implica fabricar contra pedido en lugar de hacerlo contra stocks.
Hasta hace poco, las fábricas de automóviles tenían forma de gran ladrillo, totalmente rectangular y muy alargado. Las nuevas factorías, por el contrario, trazan figuras geométricas en las que brazos laterales de uno u otro tipo penetran como cuñas en la nave central. Tales cambios constituyen adaptaciones funcionales por cambios sustantivos en el proceso de fabricación del automóvil. Si bien es una industria que tiene un grado razonable de "madurez", es al mismo tiempo un sector que vive una "revolución silenciosa".
Aquella revolución deriva de fabricar cada vez más contra pedido en lugar de hacerlo contra stocks. Es un paso aún más radical que el just-in-time puesto en marcha hace algunos años, porque el coche se fabrica casi a medida del cliente, que elige entre un número enorme de variaciones que singularizan el vehículo, entregándose semanas después de formulado el pedido.
Estas ideas aparecen en el libro del Centro Internacional de Investigación Logística (CIIL, Iniciativa IESE-Mecalux) sobre la evolución de las operaciones en el sector del automóvil que ha dirigido el profesor del IESE Federico Sabrià y del que son autores Jan A. Nikolaisen, Julián C. Longstaff y Arturo T. De Zan, con la colaboración de Miquel Cardona. Este equipo de trabajo ha visitado las fábricas de Nissan (Barcelona), PSA (Peugeot y Citroen) (Madrid), Ford Motor (Valencia), SEAT (Martorell) y Smart (Hambach - Lorena) y estudiado las estrategias de gestión y comercialización de cada una de las compañías.
Para enmarcar la actualidad del sector, repasan los grandes hitos de la evolución histórica de las operaciones productivas en automoción, detallando los conceptos de "fabricación en serie" de Ford, el "sloanismo" de General Motors o el "toyotarismo" nipón, para desembocar en la situación actual, en la que las estrategias son mixtas, tomando lo mejor de cada enfoque y sin asegurar que una sea mejor que otra. Todas coinciden, sin embargo, en que es más adecuado migrar de una política contra stock hacia una que sea cada vez más contra pedido.
Por otra parte, las grandes fábricas de automóviles tienden a externalizar o subcontratar una gran parte de componentes e incluso módulos enteros del vehículo, centrándose de forma preferente en el montaje, en la fase final, que es lo que añade mayor valor al producto, con especial importancia del diseño. Este fenómeno hace pensar a algunos analistas en la posibilidad de que en el futuro "los fabricantes de coches puedan convertirse en empresas de gestión de marcas más que de manufacturas".
Imposible predecir la demanda
Prever la demanda se ha vuelto prácticamente imposible para el fabricante por la enorme variedad y consiguiente fragmentación de los tipos solicitados, por lo que la estrategia de los industriales ha pasado de "producir para disponer de existencias" a la de "no fabricar el vehículo sino hasta tener el pedido concreto del cliente".
Los fabricantes entienden que ello les representa una cierta ventaja competitiva, medida desde sus estrategias particulares (p. ej.: gestión de la calidad, trabajo en equipo, acuerdos con proveedores, etc.) Por un lado, el cliente está dispuesto a pagar algo más por un coche con una configuración de especificaciones que él mismo ha seleccionado, tales como modelo, colores externo e interno, cilindrada o diversos complementos. Por otro, fabricar sobre pedido reduce las existencias y elimina el riesgo de producir vehículos que en el futuro resulten obsoletos.
Si en el plano teórico fabricar contra pedido parece casi un ideal, en la práctica no es tan sencillo porque exige una gran flexibilidad de fabricación que no siempre es fácil de asumir, manteniendo al mismo tiempo la rentabilidad del negocio y realizando la entrega del coche al cliente en el plazo acordado. Con los continuos cambios en especificaciones y modelos resulta más difícil planificar la producción. Cierto que la informática permite introducir con relativa facilidad los cambios de lote de fabricación, incluido el de un solo vehículo, pero no por ello desaparecen del todo los tiempos muertos, especialmente los referidos a las operaciones (p. ej.: ciclos de producción, tiempo de almacenamiento del vehículo terminado, etc.). Además, se suman problemas humanos como los horarios laborales, lo cual hace fluctuar el volumen de las plantillas, obliga a una gran versatilidad al personal y es más complejo controlar en cuanto a los costes de producción y la organización de la cadena de suministros, especialmente en materia de piezas y módulos. Por esto último, el impacto de este cambio incluso puede ser mayor en los suministradores de la industria auxiliar que en la empresa final.
Los fabricantes afrontan las dificultades en base a compartir componentes entre diversos modelos, utilizar procesos de fabricación similares y piezas estandarizadas. A la vez, exigen tener a los proveedores de componentes cada vez más cerca de la planta, prácticamente en el mismo polígono industrial en que se encuentra la fábrica de automóviles, para que de forma inmediata puedan suministrar las piezas o módulos necesarios en el instante adecuado, en la cantidad correcta y siguiendo una secuencia planificada.
Los autores del estudio se han encontrado con que los fabricantes no sienten especial angustia por las exigencias de la producción contra pedido. La mayoría de empresas pueden fabricar el coche en un plazo de ocho días desde la recepción del pedido y algunos en un plazo aún inferior. Sin embargo, el transporte del coche terminado hasta el cliente puede tardar al menos dos semanas. Todo indica que los fabricantes superan con buena nota la diversificación del mercado y fragmentación de modelos, pero el equipo del CIIL apunta que "no parece muy probable que el sector pueda hacer frente, a largo plazo, a la combinación de sobrecapacidad y precios bajos que se da en la actualidad".
El libro concluye señalando un aspecto en que todos los industriales coinciden: la necesidad de establecer alianzas cada vez más convenientes entre fabricantes y proveedores, de modo que la capacidad de los primeros en reaccionar frente al mercado y sus fluctuaciones sea cada vez más ágil y eficiente. En efecto, sin una gestión eficaz de la cadena de suministro, todas las interrelaciones e interdependencias serán muy complicadas de integrar dentro de un escenario de mercado cada vez más exigente y competitivo.